Soft Magnetic Material Technology
Wire Technology
Winding Technology
On high power applications, how to improve the magnetic materials performance is a key fact for high -power and high-frequency transformer and reactor design, which can lead to very good cost performance at rather small size.
By fully understanding both the magnetic requirements from circuit topology of most popular power converter applications and material spec mechanism from manufacturing process, collaborating with the world class soft magnetic material experts, it comes possible to extend the material performance better
Technical Frontier
1. MHz class supper low core loss new ferrite material
2. New generation ferrite for more than 50KW LLC power converter
3. New FeSi powder core material for very high power boost reactor
4. High performance powder core for FCV compressor driver
5. High permeability ferrite core for high current edgewise winding EMC choke
New Ferrite Material
Advaced Powder Core
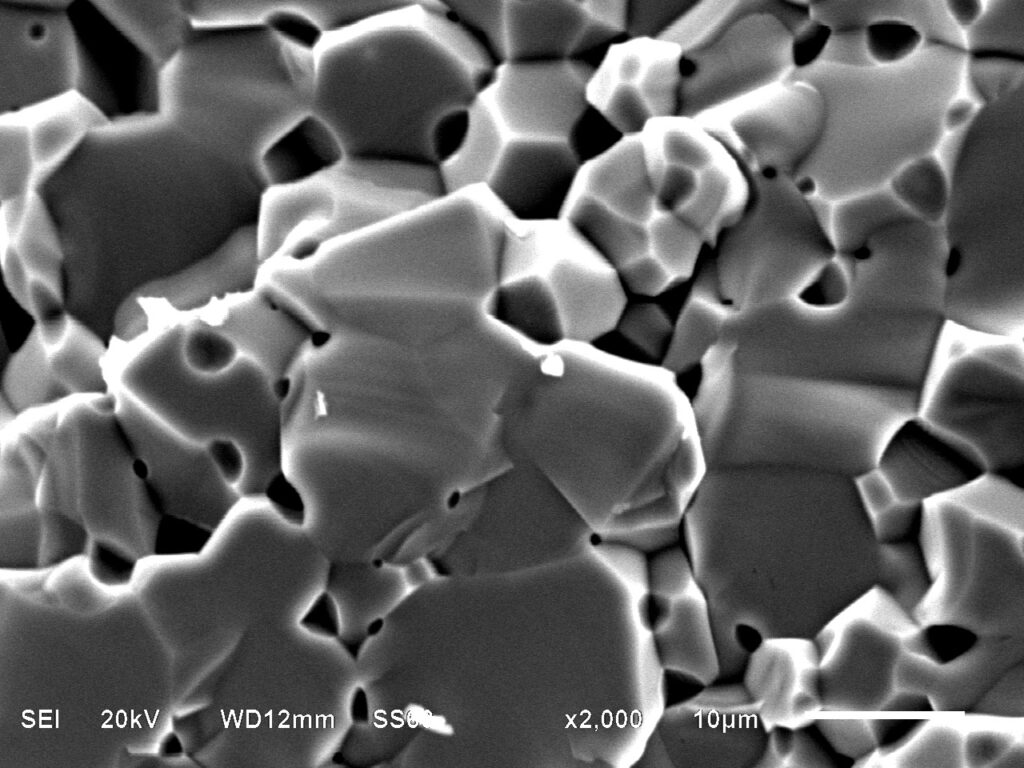
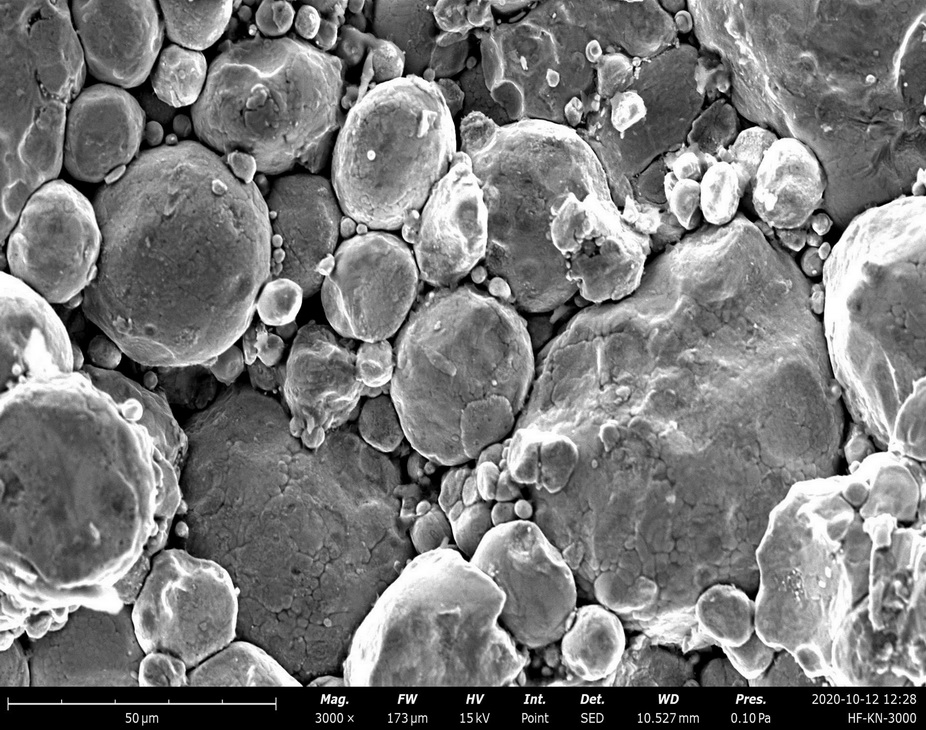
In the application of large power, high -voltage, and high power density, there is a bottleneck if only using a normal magnet wire trying to extend advanced winding technology better.
By designing magnet wire shape, improving wire specifications such as the insulation of film characteristics, wire mechanical characteristics, copper conductivity , and the thermal conductivity characteristics, a new technical world for advanced high power magnetic component design is opened.
Technical Frontier
1. Reinforced insulation lizz wire for high power density LLC transformer
2. Flat magnet wire better for water cooling and oil cooling winding
3. PEEK flat magnet wire for 800Vdc bus line application
4. Reinforced insulation PEEK flat magnet wire for edgewise winding
5. Super aspect ratio flat magnet wire for edgewise winding
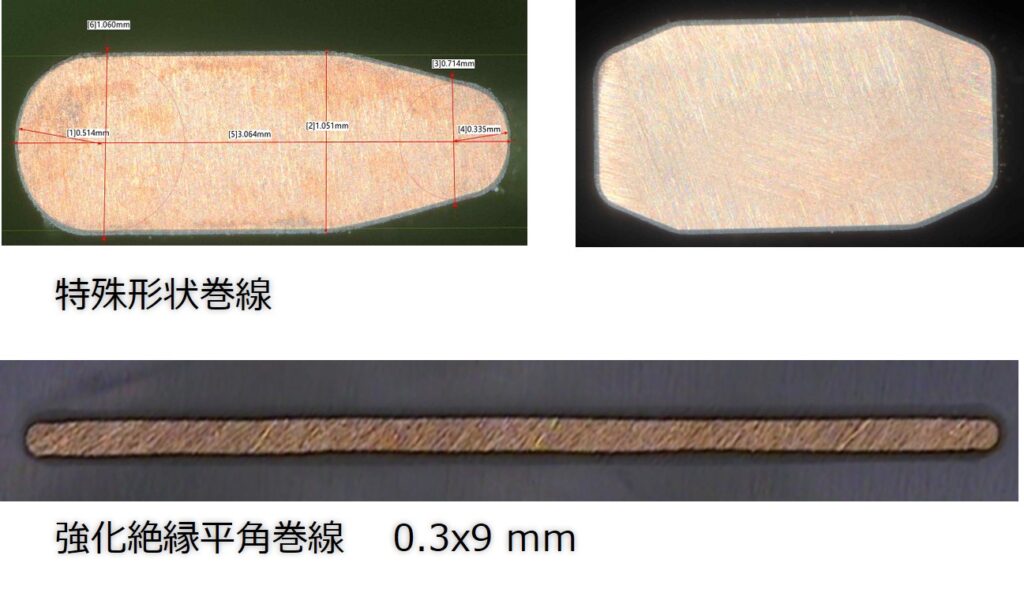
We build best magnetic circuit structure and optimize coil design for less AC loss, better heat dissipation, good insulation, much smaller size and volume at all power magnetic components.
In addition, as a part of core technology for our product design, applying automatic production processing processes more smoothly in products and manufacturing equipment becomes so important to cut product cost and get better quality.
Technical Frontier
1. Smallest angle bending technology on 90° right angle edgewise winding
2. Super aspect ratio (30:1 or larger) reinforced insulation edgewise winding technology
3. Automatic winding technology for high speed with very small dimension tolerance (±0.1㎜ flatness over 1000㎟ square coil)
4. Tiny gap dimension winding technique between winding wires(<0.1mm)
5. High-speed, high-precision, low cost peeling technique
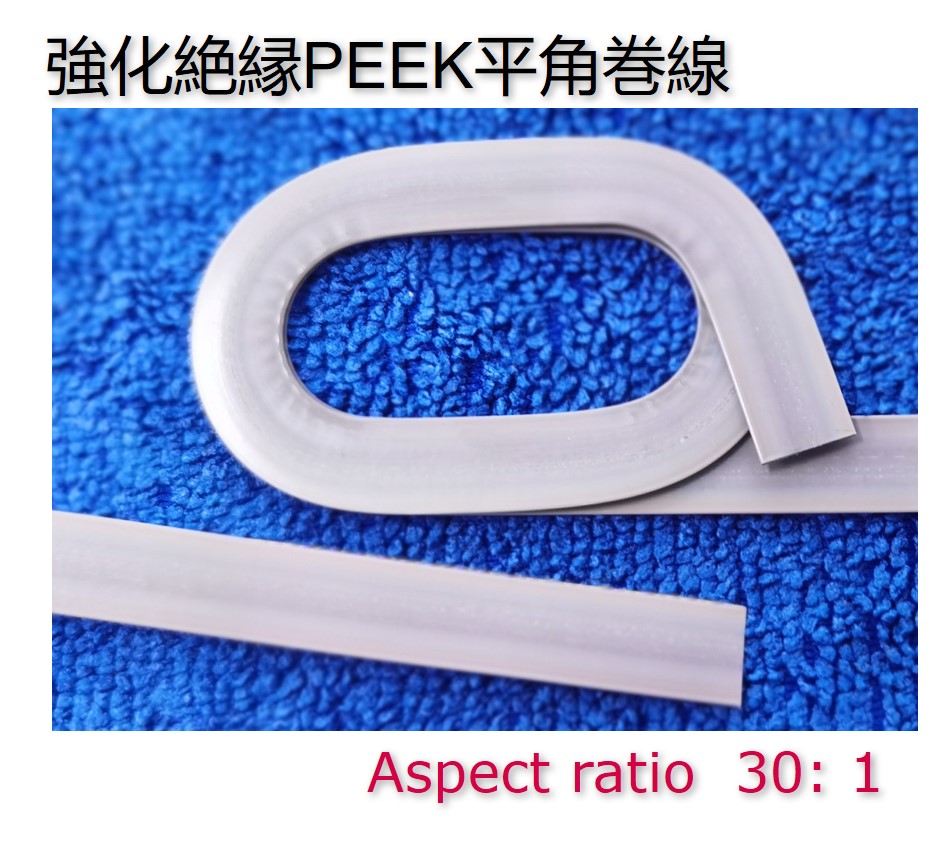
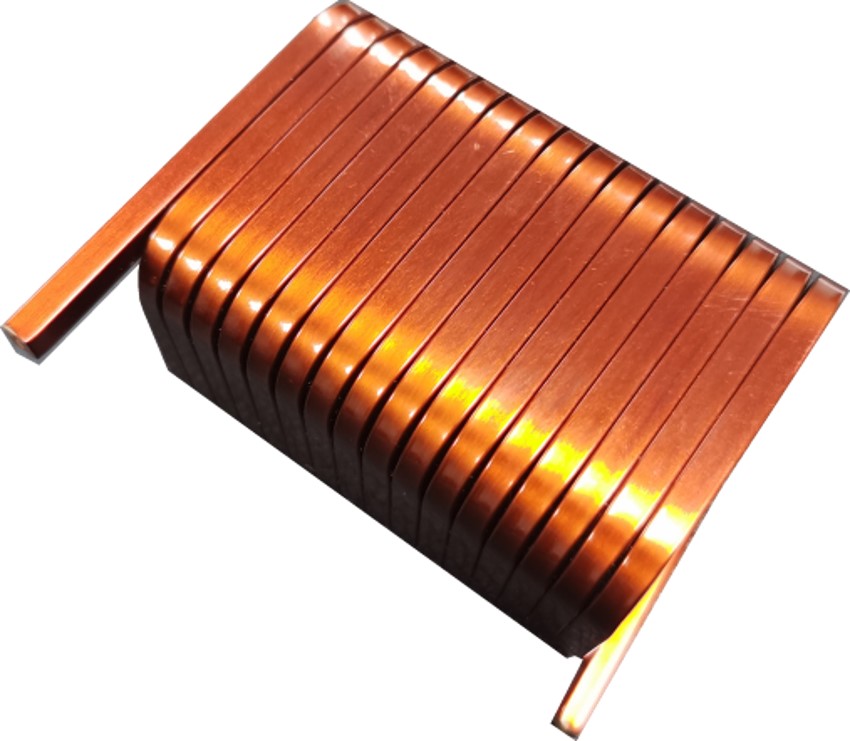

Magnetic Circuit Technology
By applying creative innovation of unique coil and core design, optimzing magnetic circuit to build best inductance-current curve and the best cost performance, the state-in-art magnetic circuit technology provides a compact part dimension with least AC loss both on coil and core, also can improve EMC performance.
Technical Frontier
1. Technology on improvement the DC Bias characteristics of the inductor by optimizing magnetic core materials and shapes
2. Advance technology of core loss and coil loss balance control by a best hybrid magnetic ciucult structure design
3. Optimization of insulation structure and heat dissipation design for the best cost performance desgn
4、Composite magnetic circuit technology
5. Edgewise winding EMC choke technology for high current application
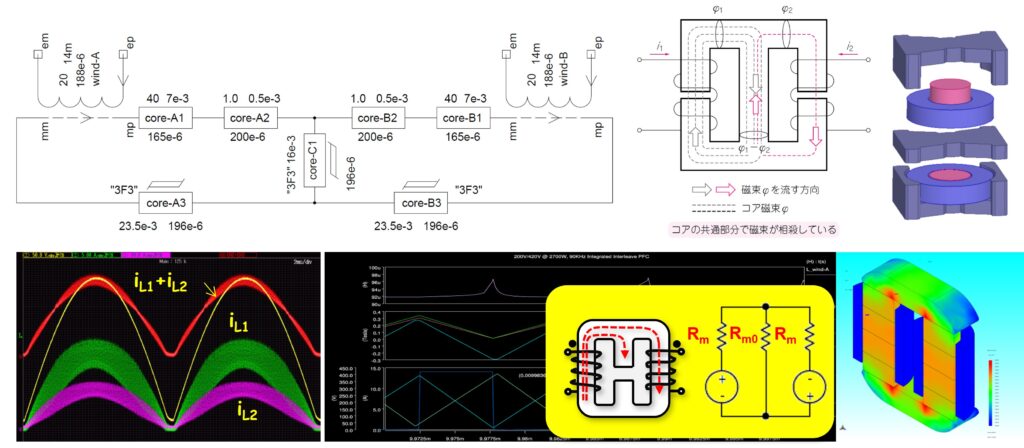
Injection molding Technology
Integral PPS injection molding technology is an important way of designing parts with fewer BOM items while achieving both heat dissipation, insulation, mechanical durability, and convenient mounting methods.
In order to building a good heat dissipation for power reactor and power transformer, it is the best way to design the every winding outer surface exposed to the outside by the integral PPS injection molded technology, while the PPS material being tightly filled without gaps between the coil and the core.
Technical Frontier
1. Technology that enables injection molding even in tiny gaps between the core and the coil
2. Bobbinless PPS injection molding technology to keep less material items on BOM that can benifit for product cost performance
3. Low temperature injection molding technology
4. Temperature detection technology for integral injection molding parts
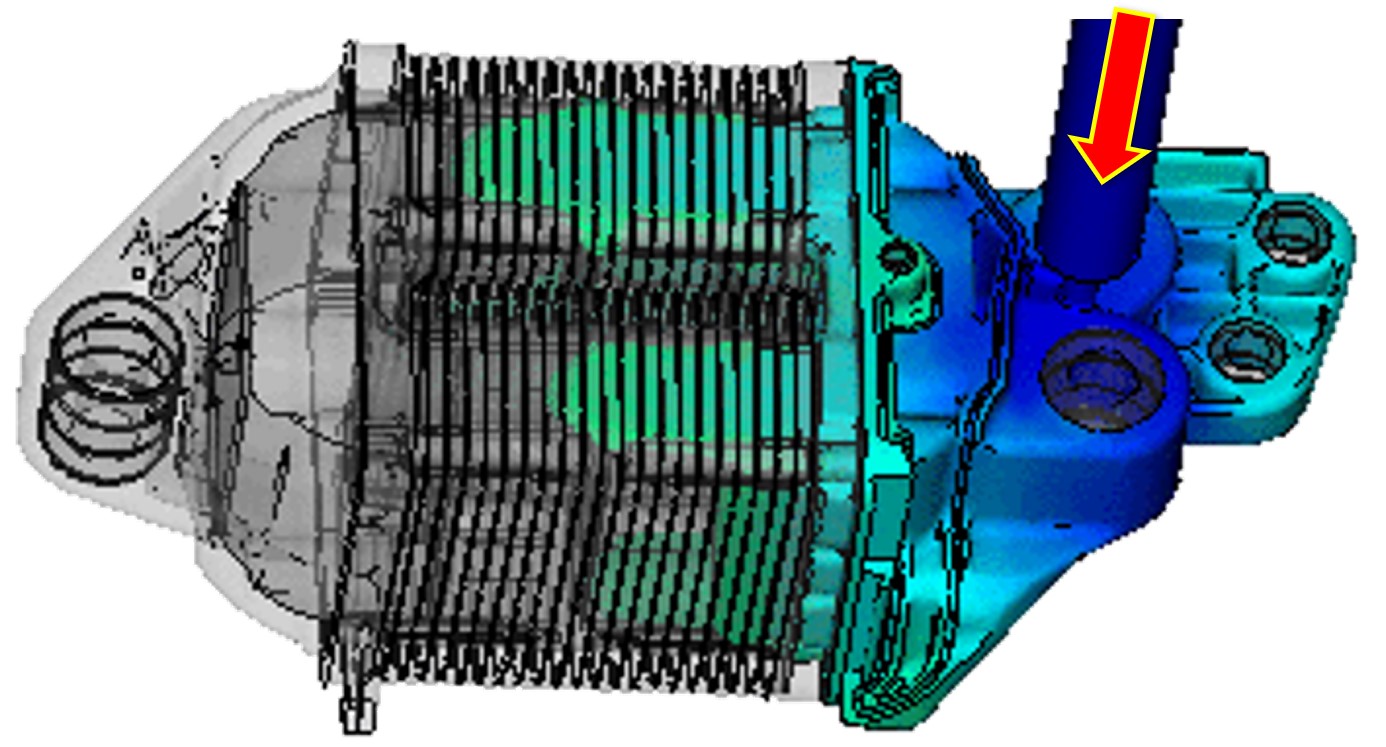
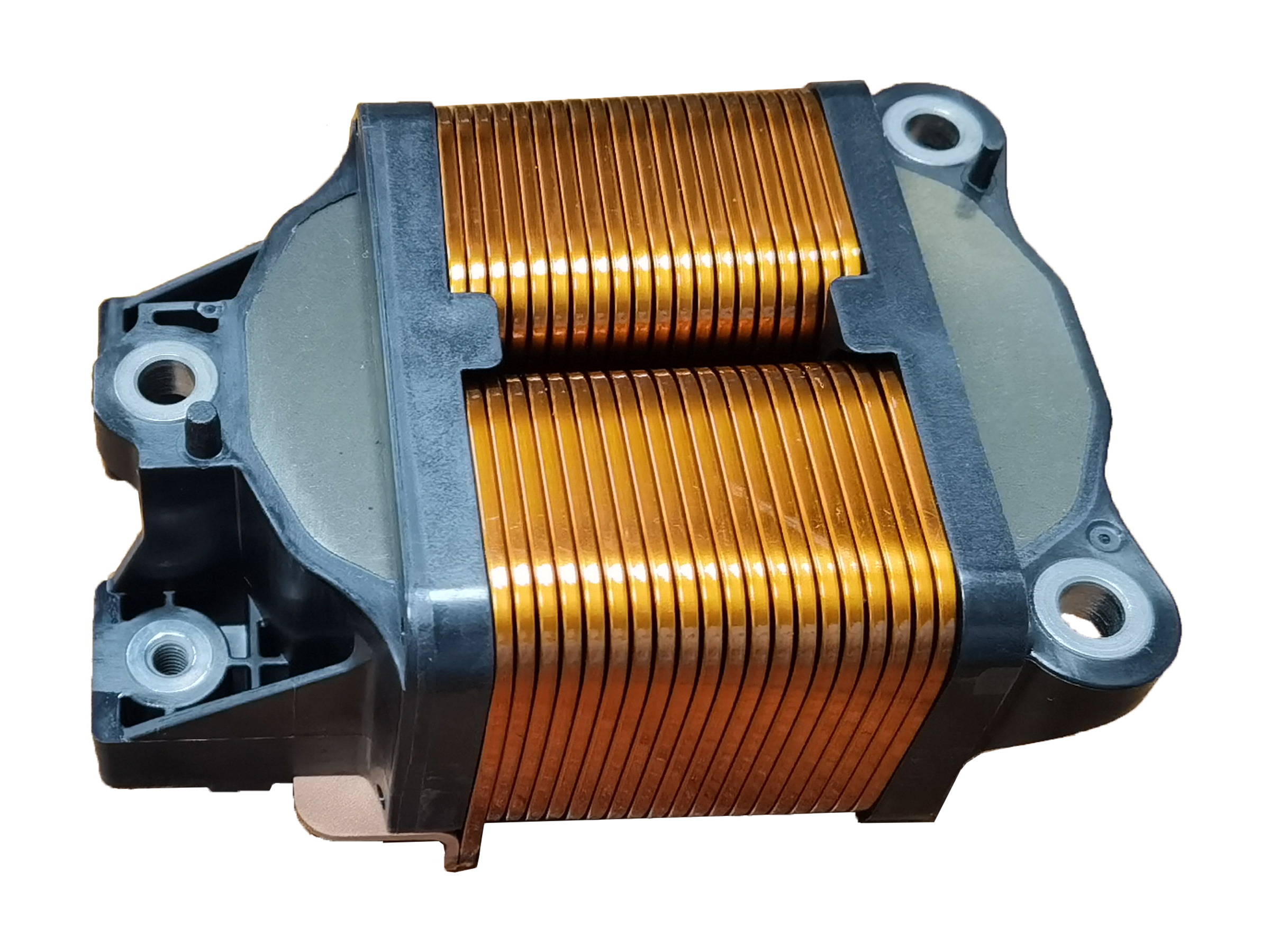
.
Coil Temperature Sensing Technology Design Samples
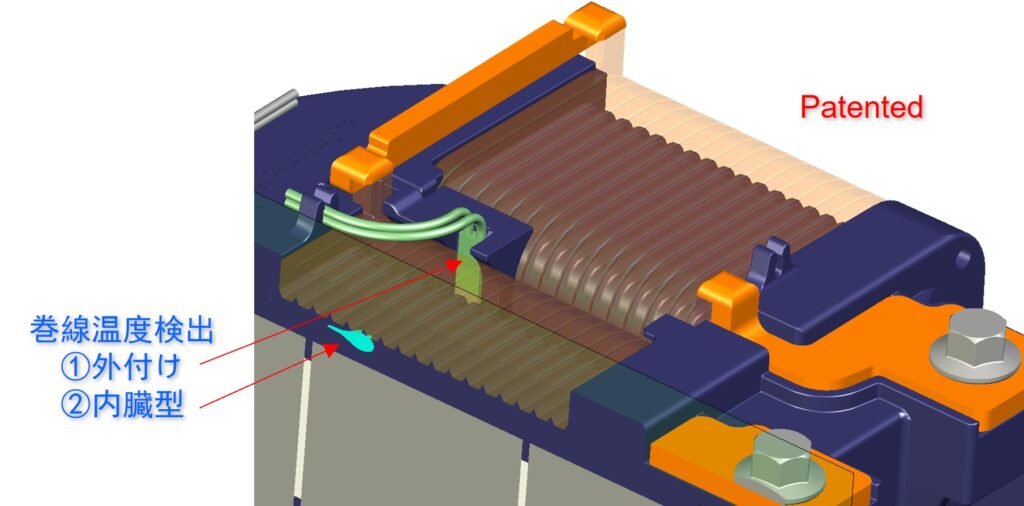
Pride of technician ♪
